Пресс-форма для литья пластмасс под давлением: особенности конструкции и технология изготовления
Пластик сегодня пользуется очень большой популярностью в качестве сырья. Изделия из этого материала встречаются практически во всех сферах деятельности человека. Например, детали автомобилей, самолетов, станков, детские игрушки, тара и прочая продукция изготавливается из пластика. Серийное производство пластиковых изделий — довольно сложный технологический процесс, который осуществляется на термопластавтоматах (ТПА) методом литься под давлением. Основным узлом термопластавтомата и в то же время его сменной частью (оснасткой) является пресс-форма. В этом материале рассмотрим, как устроена пресс-форма и как литьевая оснастка изготавливается.
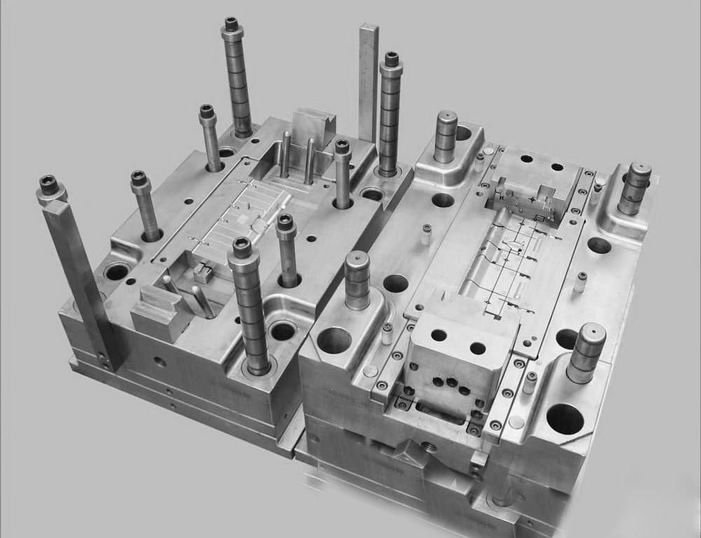
Пресс-форма: что это такое и как устроена
Пресс-форма — это литьевая оснастка, которая задает конфигурацию отделяемого изделия. Она имеет полость, куда заливается жидкий пластик под давлением. Форма и размеры этой полости и определяют внешние данные конечного изделия.
Раньше для одного термопластавтомата устанавливали только одну пресс-форму. Однако сейчас рынок пластиковой продукции развивается, и производители в целях увеличения предлагаемого ассортимента используют около 5-6 оснасток (пресс-форм) для одного ТПА. Благодаря этому компания может поставлять на рынок большое количество видов продукции.
Пресс-форма имеет сложную конструкцию, состоит из следующих элементов:
- плиты. Они образуют внешний каркас конструкции. Бывают задние, нижние, внешние, боковые плиты;
- формообразующие детали. К этой группе относятся те "запчасти" пресс-формы, которые при смыкании оснастки образуют полость, куда заливается жидкий пластик;
- литниковая система. Это группа деталей, которые обеспечивают поступление жидкого пластика в полость;
- охлаждающая система. Это каналы, по которым циркулирует холодильный агент и охлаждает пресс-форму;
- система выталкивания. Жидкий пластик поступает в полость пресс-формы и охлаждается, после чего затвердевает. Готовое изделие выталкивается специальными деталями - толкателями.
Из всех перечисленных выше деталей стоит подробнее остановиться на формообразующих элементах. При смыкании частей формы эти элементы создают ту самую полость, куда заливается пластик. К формообразующим деталям относятся:
- пуансон. Это подвижная часть пресс-формы. Она двигается и примыкает к неподвижной части, образуя полость;
- матрица. Это неподвижная часть оснастки;
- ползуны. Двигаются перпендикулярно плоскости, по которой происходит смыкание. Ползуны нужны для создания сложных боковых поверхностей изделия;
- знаки. Это съемные детали, которые нужны для создания дополнительных отверстий, пустот внутри изделия и пр.
Литниковая система пресс-формы может быть холодноканальной и горячеканальной. В первом случае жидкий пластик по специальным каналам поступает в полость. Это сравнительно простой вариант, но имеет существенный недостаток: после изготовления отливки придется в ручном режиме подрезать литник, а пластик, который остался в каналах в затвердевшем состоянии, придется утилизировать. Горячеканальная система куда сложнее, но лишена этого недостатка. В этом случае устанавливаются специальные сопла, которые впрыскивают пластик в полость формы.
Как происходит изготовление пресс-форм
Литьевая оснастка — сложная деталь, которая изготавливается не за один день. От качества пресс-формы зависит и качество выпускаемых далее изделий. Поэтому пресс-форму нужно заказывать в проверенных компаниях, а лучше на российском рынке. Лидером российского рынка является компания «Метропласт Инжиниринг». Она не только изготавливает пресс-формы на заказ, но и предоставляет ряд сопутствующих услуг и дает пожизненную гарантию на литьевые оснастки.
Итак, производство пресс-формы — сложный процесс. Состоит он из следующих этапов:
- подготовка чертежей и 3D-модели;
- сборка пресс-формы;
- доводка и испытание.
Рассмотрим их подробнее.
Подготовка
Этот этап полностью представляет собой работу за компьютером. Специалист создает 3D-модель будущей пресс-формы, основываясь на подготовленных чертежах и данных, полученных от заказчика. 3D-модель имеет важное значение — от нее зависит конфигурация будущей пресс-формы. Подготовка трехмерной модели происходит на компьютерных CAD-системах.
Сборка
На этом этапе все составные части литьевой оснастки (о которых мы рассказали выше) изготавливаются на специальных станках с числовым программным управлением, что позволяет гарантировать точность и минимизировать участие человека.
Обработка включает в себя следующие процедуры:
- Отжиг. Данная процедура позволяет снять остаточные напряжение с заготовки.
- Черновая обработка. Обычно проводится на фрезерных станках с ЧПУ, в ходе чего снимается часть материала с поверхности.
- Нормализация. Способствует снятию напряжения с металла.
- Получистовая обработка. Поверхность готовится к окончательной обработке.
- Закалка.
После производства всех деталей происходит сборка. Это полностью ручной процесс. В ходе сборки также может возникнуть необходимость провести подгонку, полировку и пр. Еще очень часто во время сборки проводят хромирование — процесс, который позволяет создать поверхность высокой твердости. Хромированная пресс-форма служит намного дольше, чем обычная.
Его итогом является почти готовая пресс-форма. Остается только выполнить доводку и провести испытание.
Доводка и испытание
Доводка проводится в рамках доведения пресс-формы до требуемых и точных параметров. Обычно специалисты проводят ручную механическую обработку. В результате литьевая оснастка будет доведена до требуемых параметров.
Следующий этап — испытание. Обычно оно проводится на специальных испытательных термопластавтоматах и позволяет выявить ошибки и неточности. Если таковые будут обнаружены, то специалисты проводят повторную механическую обработку.
В рамках испытаний также могут провести испытание тестовой партии пластиковой продукции.